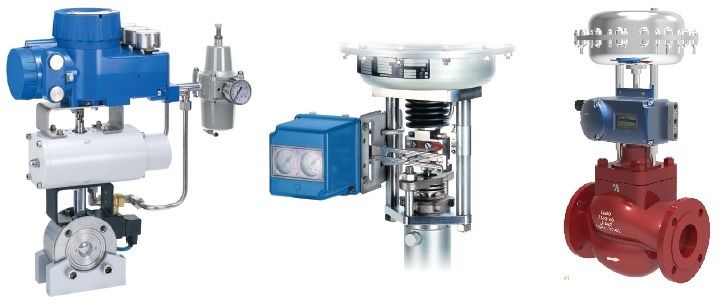
Choosing the right valve positioner for your application can have a big impact on process control, equipment lifespan, and maintenance efficiency. Here's a practical guide to help you make the right choice:
How to Choose the Right Valve Positioner for the Right Application
1. Understand the Application Requirements
Start by defining:
- Process type: Is it a simple open/close (on-off) application, or does it require precise control?
- Improved Control Accuracy: Digital positioners can compensate for valve friction, hysteresis, and wear, ensuring more stable and accurate valve performance.
- Speed of response: Is rapid actuation required?
- Criticality: Is the valve in a safety-critical or compliance-sensitive loop?
Example: A modulating control valve in a pharmaceutical process needs higher precision and diagnostics than an on-off valve in wastewater.
Pharmaceutical, Specialty Chemicals, Food & Beverage industries require high accuracy, repeatability, and tight process control—often in compliance with GMP, FDA, or HACCP.
2. Know the Valve and Actuator Type
- Pneumatic, electric, or hydraulic?
- Linear or rotary actuator?
- Some positioners are designed for specific actuator types—match accordingly.
3. Decide on Control Signal Type
- Analog (4-20 mA) – common for analogue and digital positioners.
- Digital communication protocols – like HART, FOUNDATION Fieldbus, or Profibus if you're integrating with a DCS or asset management system.
Tip: If remote diagnostics or integration into smart systems is important, a digital positioner is the better choice. This allows for remote calibration, tuning, and troubleshooting.
A control room operator can monitor multiple valves via digital positioners from a central interface and get alerts if one drifts or fails.
If your facility is moving toward digital transformation or predictive maintenance, investing now can avoid replacement later.
4. Consider Maintenance and Diagnostics Needs
Ask:
- Do you want predictive maintenance capabilities?
- Would remote access reduce technician exposure in hazardous areas?
- Is data logging important for compliance?
Analogue positioners are simple to maintain with basic mechanical skills but they have no built-in diagnostics, so troubleshooting takes longer.
Choose a digital positioner if you want advanced diagnostics, self-calibration, or remote monitoring. They can detect early signs of issues like sticking valves, air leaks, or actuator wear and generate alerts and alarms which will help prevent unplanned downtime and reduce recurring maintenance costs significantly.
Predictive diagnostics enables servicing of valves only when needed and reducing the need for manual inspection. It reduce emergency maintenance and associated labour costs.
Digital positioners can often perform auto-calibration reducing human error and setup time.
5. Think About Environment and Conditions
- Hazardous area? You’ll need ATEX, IECEx, or other certified devices.
- Corrosive environment? Look for rugged enclosures or coatings.
- Temperature extremes? Choose models rated for the site’s ambient conditions.
Remote diagnostics cuts down on time technicians spend in the field—especially in hazardous or hard-to-reach areas.
6. Evaluate Budget vs. Long-Term Value
- Analog positioners have a lower upfront cost but higher ongoing maintenance.
- They have fewer features and are a great fit for basic control loops and applications
- Digital positioners are more expensive initially but offer long-term savings through auto-calibration, diagnostics, remote monitoring resulting in reduced downtime, fewer calibrations, and improved control.
Consider the cost of failure or poor performance in your process. If a valve controls a critical path or compliance-sensitive output, investing in a higher-end positioner often pays for itself quickly.
Choose analogue for simple or cost-sensitive loops, and digital for critical or high-precision applications where the extra investment pays off.
DP-Flow are Partners to Schneider Electric for process instrumentation