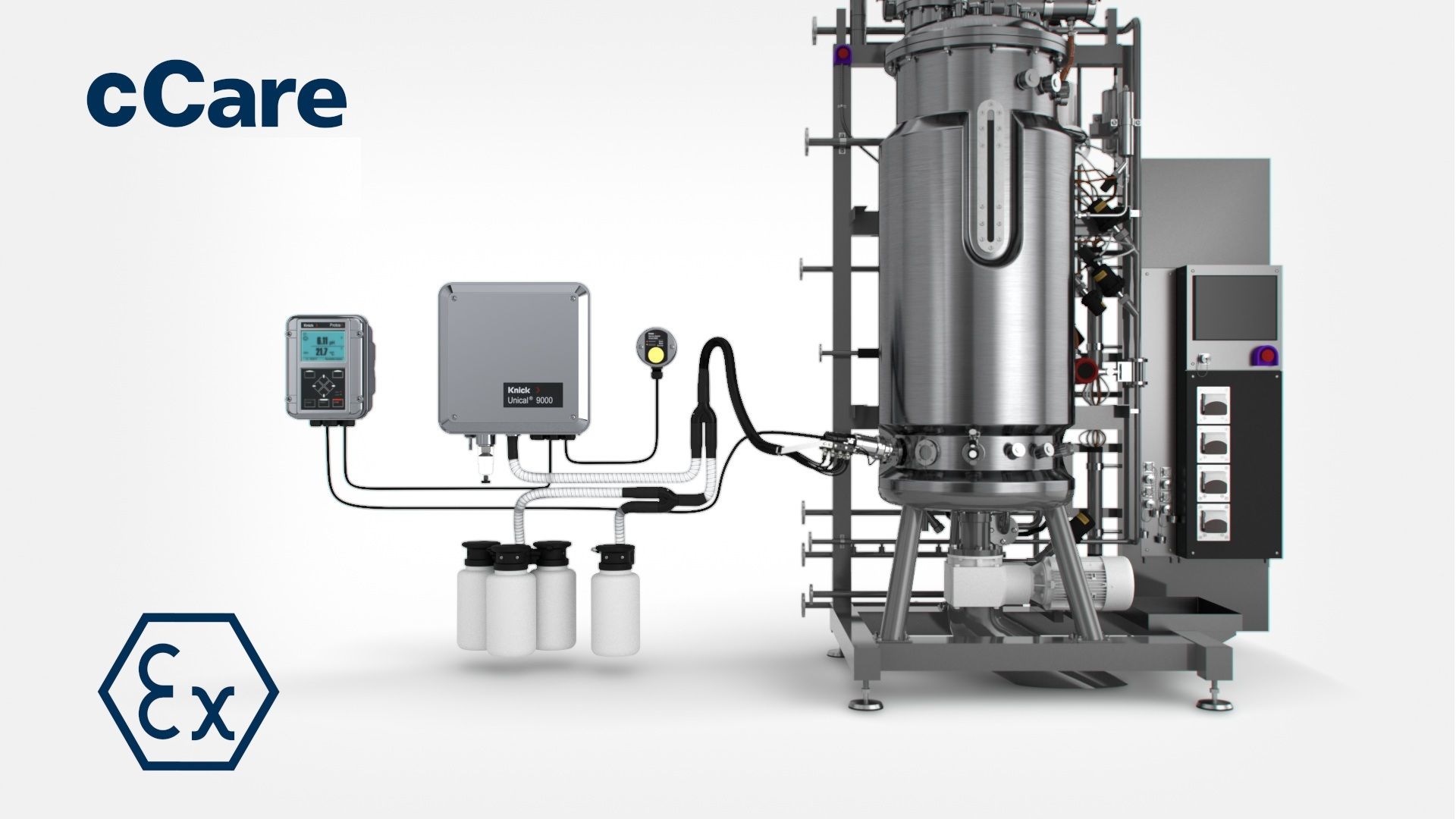
Maintaining accurate static pH measurements in industrial settings can be a resource-heavy challenge. Between constant maintenance, repeated calibrations, and frequent sensor replacements, it's no surprise that many plants are turning to automation to save time, money, and improve safety.
Why Automated pH Cleaning and Calibration Systems Are a Game-Changer for Industrial Operations
If you're still relying on static online systems that require manual sensor handling, it might be time to rethink your approach. Here’s why automated pH cleaning and calibration systems are quickly becoming the standard in critical applications.
When Static pH Loops Fall Short
Static pH measurement systems are widely used and generally effective—but only up to a point. In more extreme process environments, they can become unreliable and costly to maintain. High temperatures, abrasive slurries, and aggressive pH swings often lead to sensors wearing out quickly.
Maintenance teams are then left juggling frequent sensor replacements, compliance risks, and safety concerns particularly when hazardous process conditions require personnel to use personal protective equipment or take extreme precautions to protect themselves while working with the pH loop.
And if the pH loop is tied to regulatory compliance (such as environmental discharge limits), inaccurate readings could mean fines—or worse, a full system shutdown.
The Automated Advantage
1. Hands-Off Cleaning and Calibration
With static systems, techs often have to travel to the sensor site, pull it from the line, clean or calibrate it, and reinstall it—sometimes daily. That’s a lot of downtime and manpower.
Automated pH systems handle cleaning and calibration on a set schedule. Technicians can also trigger cycles manually without physically accessing the process line. This drastically reduces maintenance time and increases measurement uptime.
2. Longer Sensor Life, Fewer Replacements
One of the biggest benefits of switching to an automated pH system is reducing sensor wear and easing the pressure on maintenance budgets. In tough process environments—where you’re dealing with extreme pH swings, high temperatures, or abrasive slurries—sensors can burn out fast. In some cases, they need to be replaced weekly, or even daily.
Manual cleaning and frequent handling only make things worse. Without proper procedures or spare sensors on hand, damage and unexpected process upsets become common.
Automated systems solve this by running scheduled maintenance cycles that automatically retract, clean, calibrate, and reinsert the sensor. By protecting the sensor from harsh conditions and ensuring consistent upkeep, automation significantly extends sensor life and cuts down on replacements—keeping operations smooth and costs in check.
3. Improved Safety for Your Team
Working with pH sensors in hazardous environments often requires technicians to wear specialized PPE—acid-resistant suits, supplied air systems, and follow lengthy shutdown procedures just to access the sensor safely. These tasks aren’t just time-consuming—they can also put workers at risk.
Automated pH systems drastically reduce these safety concerns by performing most maintenance tasks automatically. Cleaning and calibration cycles happen without human intervention. When a sensor does need replacing, the system retracts and isolates it first, cleaning it thoroughly to make it safe for handling. This means minimal exposure to the process and far less time spent in dangerous areas.
With automation in place, technicians no longer need to physically enter the process unit for routine maintenance, making your operation not just more efficient—but much safer, too.
4. Stay Ahead of Compliance Requirements
Maintaining regulatory compliance is critical—especially when it comes to wastewater, scrubbers, or any effluent monitoring. A single error in pH measurement can result in hefty fines or even forced shutdowns.
Automated systems ensure measurement accuracy through consistent, scheduled calibration and cleaning. Even better, these systems support remote monitoring and diagnostics, giving operators real-time visibility into sensor performance. Calibration logs are stored automatically and can be easily accessed for environmental permit reporting.
This added visibility and control significantly lowers the risk of noncompliance, helping your team stay ahead of permit requirements and avoid costly disruptions.
5. Where Automated Systems Make the Biggest Impact
Automated pH systems are versatile and valuable across a wide range of industries, especially where process conditions are harsh or accuracy is critical. Ideal industries include:
- Refining
- Pharmaceuticals
- Food & Beverage
- Petrochemical
- Agriculture
And the types of applications that benefit from automation are just as broad:
- Outfall/Effluent Monitoring
- Wastewater Clarifiers
- Neutralization Skids
- Wet Gas Scrubbers
- Flotation Cells
- Sugar Carbonation
- Ethanol Corn Mash Slurry
- Flue Gas Desulfurization
Take wastewater treatment, for example—sticky substances often coat sensors, reducing accuracy and requiring frequent cleaning. Frequent handling in these environments leads to probe damage, costly downtime, and unreliable data. Automated cleaning and calibration not only prevent these issues, they also ensure the pH readings remain accurate and consistent with less intervention.
Final Thoughts
No matter the challenge—whether it's excessive sensor replacement, too much technician time spent on manual cleaning to prevent drift, or hazardous working conditions causing a safety concern —automated pH cleaning and calibration systems offer a powerful solution.
They extend sensor life, reduce labor costs, improve safety, and ensure compliance—all while delivering reliable, accurate measurements you can count on.
If your pH loop is creating more problems than it’s solving, automation could be the upgrade your process needs.